Ok, we now cover both kinds of conversions, so here is the stock bug pan.
The hard part of converting the stock torsion is that the inner IRS pivot has
to ride just inside the horn. While a good cut would work, we did not want
to have to scab on a bunch of extra material or have the horn weaker because of
missing support. So started the time-consuming job of fitting the pivot
into the horn.
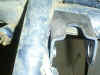
We started with a basic shape cut out on cardboard then transferred and cut
with the plasma cutter. Then we did a test fit, grind, test fit, grind,
hammer, grind, grind, hammer, test, scratch head, test, then some more
grinding. It may take some time but getting a good fit saves a lot of work
later. The idea is to have the inner pivot fit easily so it does not twist
the jig and yet be able to be welded all the way around. If there are big
gaps, material needs to be added to fill it in and make it all rigid again.
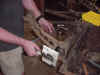
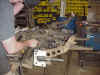
The finished product should look very clean without a bunch of gaps.
There is only one area (the first one we cut) that we will have to fill
in. Other than that the conversion went off without a hitch.
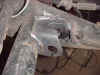